I’m tellin’ ya. I have more stupid little projects that I have lined up for myself than I could ever get done in ten years.
But one of them is finally done.
There may be one, maybe two of you guys that have been around long enough without finally saying enough with this moron, who may remember a couple years ago I posted about this weird and I guess very expensive drill press that I found at a local Goodwill for under $15.
$13.50 keeps sticking in my head for some reason.
It looks exactly like this one, except mine has a little work table on it.
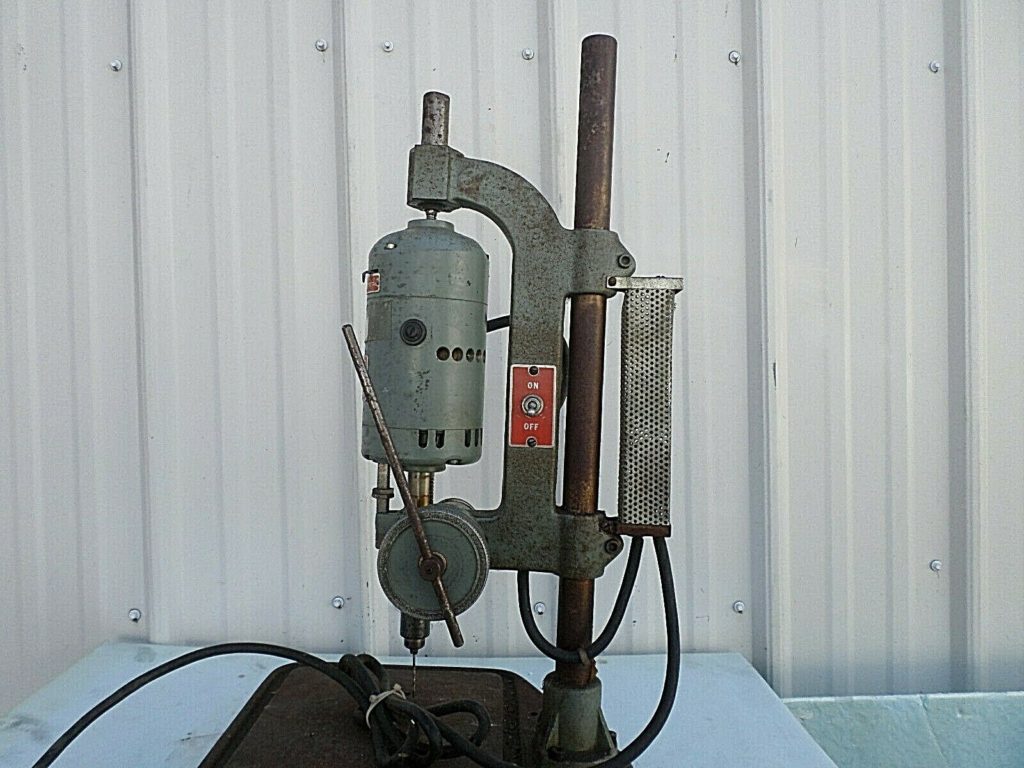
I literally had no idea what it really was, I saw it was some kind of weird drill press for under twenty bucks and threw it in the cart.
Um, yeah, about that.
After I got it home and stuffed out in the garage I started looking at it and I’m like what the fuck is this thing?
So I Googled it.
Holy Fuck.
Just this minute, I got on EBay and did a quick search.
For just the parts in the picture below, they are asking three fifty.
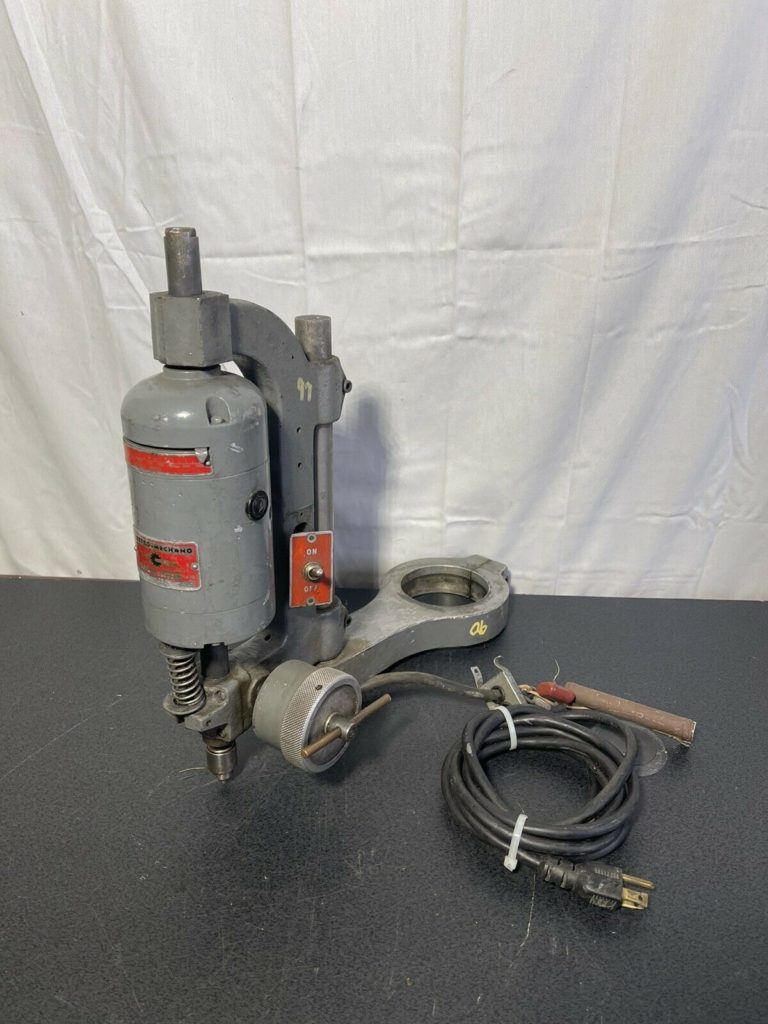
An average for all the ones I have seen have been going for about $450-$550.
I did see one they were asking $2400 for but there is always that one guy out there.
Turns out the thing is an Electro Mechanico High Speed, Sensitive Drill Press.
Basically, it’s a Super Charged Dremel motor on a stick.
1,000 to 10,000 rpm, they were advertised as being able to drill a hole smaller than a human hair.
All well and good.
It isn’t like I’m doing that kind of stuff day in and day out but whatever, I guess for under fifteen bucks I’ll keep it just because..
There was one thing about this thing that kept bugging me though.
It didn’t have a whole lot of travel, especially if you were using the table.
Sure, you probably don’t need a bunch when you are drilling needle dick bug fucker tiny assed micro holes but like pResident Poopy Pants says, C’mon Man.
So about eight months ago on one of my trips over to the Metal Supermarket, I ordered up a much longer hunk of 7/8’s round stock with the thought of one day swapping the original short one out.
I finally did just that.
First I had to get the old one out.
That turned out to be a little more difficult than I had imagined it would be.
I wound up having to use a Pitman Arm puller to get the mounting collar off the old shaft.

Then I tested the limits of the inner spindle clearance on my little Combo machine.

That 7/8’s round stock just barely fit through the spindle and the chuck.
All that just to put a small bevel on the end and then I slid it way back in the chuck, mounted a vise under the very end of the bar and used an end mill to spin a little flat spot for the set screw to land on.
After that it was clean up some bores, tappy tap tap with a Copper mallet and install the set screw,
Here’s the old bar up against the new one.

Now it has more than enough travel, there are two Allen head bolts you can loosen up and slide the whole drill motor assembly up and down the bar.

The reason I did all of this is so I could have enough clearance to be able to mount a little Chineseium X-Y table I got off Banggood cheap soon after I bought this thing.
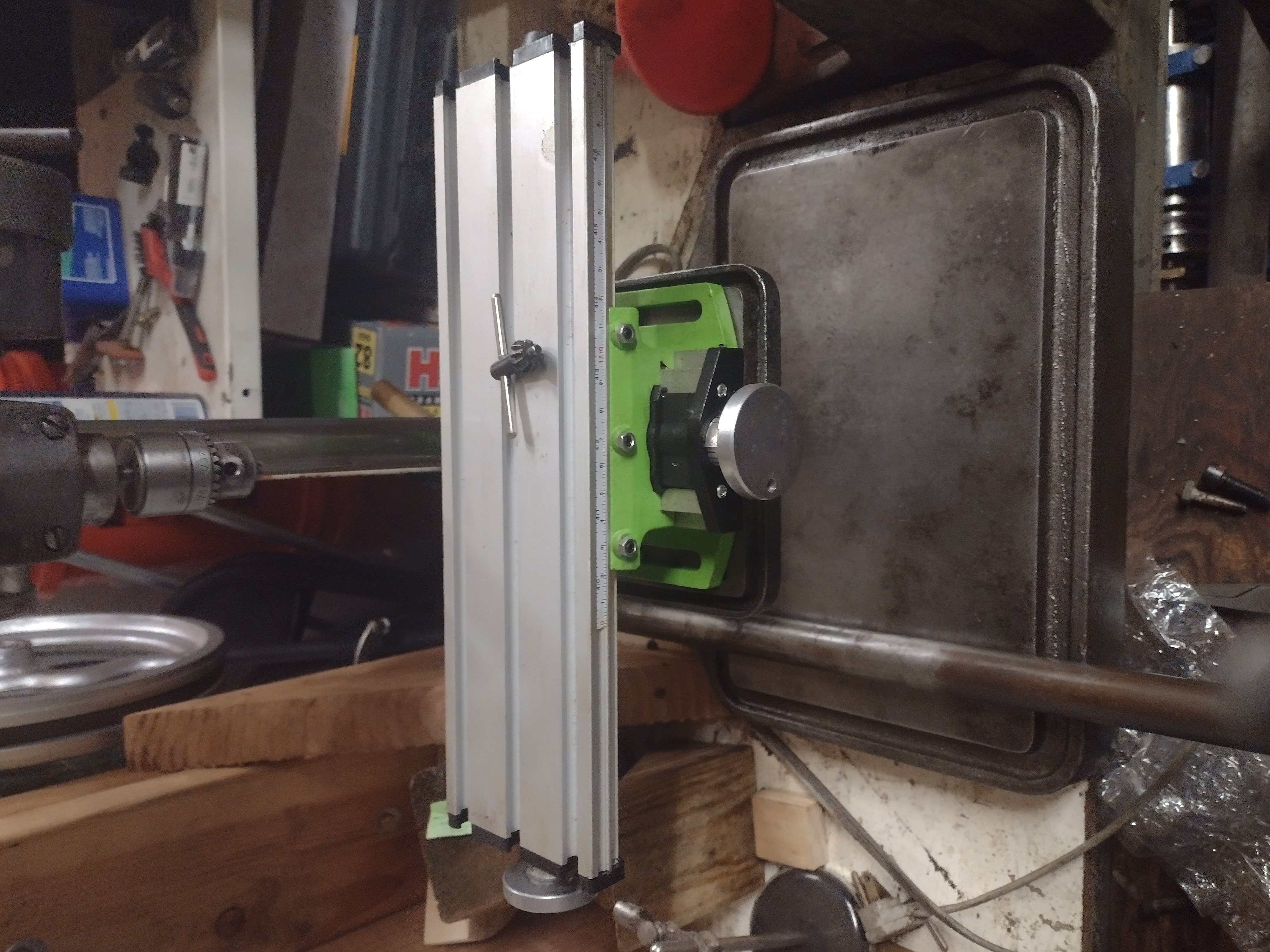
All together including the bar and the table, I have less than a hundred bucks into the thing.
So that little project is done finally.
It can go right back to collecting dust again.
BUT, it won’t be bugging me in the back of my mind every time I happen to see it anymore.
And that, is priceless.
We think alike. If I have a little project like that, it’ll eat on me until it’s done. Then it goes back and waits until I need it.
Well done! Those are really nice. I found a heavy duty one like that. It’s under the bench and needs to be cleaned to be usable. Maybe that will be another winter project this year.
Take care man.
Unfinished projects continue to be a mental load to carry around, so good on ya for reducing that.
As for the human hair thing, I knew a guy who’s outfit received a drill bit from Japan (back around the 60’s time frame) which had a diameter of that size.
They drilled a hole down through the middle of it(creating a mini-tube) and sent it back to the Japanese company.
I used one of those a couple of jobs ago (about ’85?) to drill holes in printed circuit boards. The holes weren’t hair sized, but smaller than any drill bits I have today. .015 or .020 sounds about right.
Like a lot of tools, when you need one nothing else will do.
What the heck is that? I worked around a lot of old machine shops in the cotton seed mill world. Lots of old stuff like line shaft converted machine tools. Never seen one of these interesting pieces. Word to the wise- if you remove a set screw, make sure there isn’t another one buried beneath it. Used to do that to keep crap and corruption out of the hole.
Glad I’m not the only one out there that has this problem(tool deals).
I have that same project management issue.
I see something needs done, and I’ll go get the parts.
Then I get overcome by events, and leave the bag where I set it in the garage. Soon, I’ll have 1/2 dozen bags for small projects.
I had a week off a few weeks ago, and shocked myself that I ran through all my project bags. Each one would take no time to do – like 1/2 hour and I’d wonder what the hell I dragged my feet for.
In my job, I call that “low hanging fruit”