We’ve all been there.
We’ve seen stuff get torn up, broken and mangled by certain people who have a special gift for total destruction without breaking a sweat.
Things that either shouldn’t be able TO BE broken or should at least, take extraordinary effort to do so.
Case in point.
Today at work, we got a call on the radio from a supervisor saying that this THING, got broken.
When we went to investigate, our jaws hung open at what we saw.
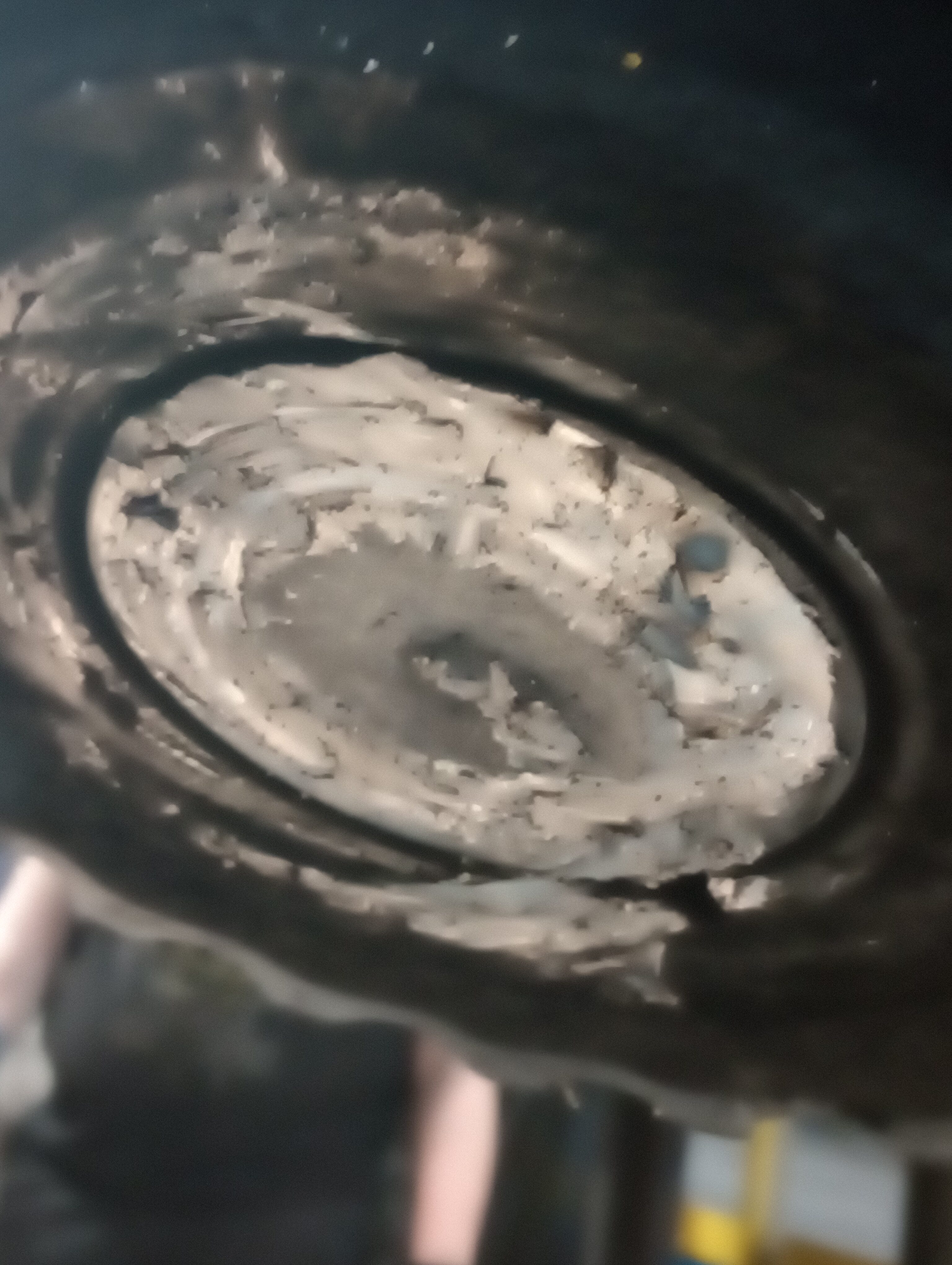
What the hell I am looking at you may ask?
That is a solid steel shaft, FOUR INCHES IN DIAMETER, broken clean in half.
This is the other end of it.
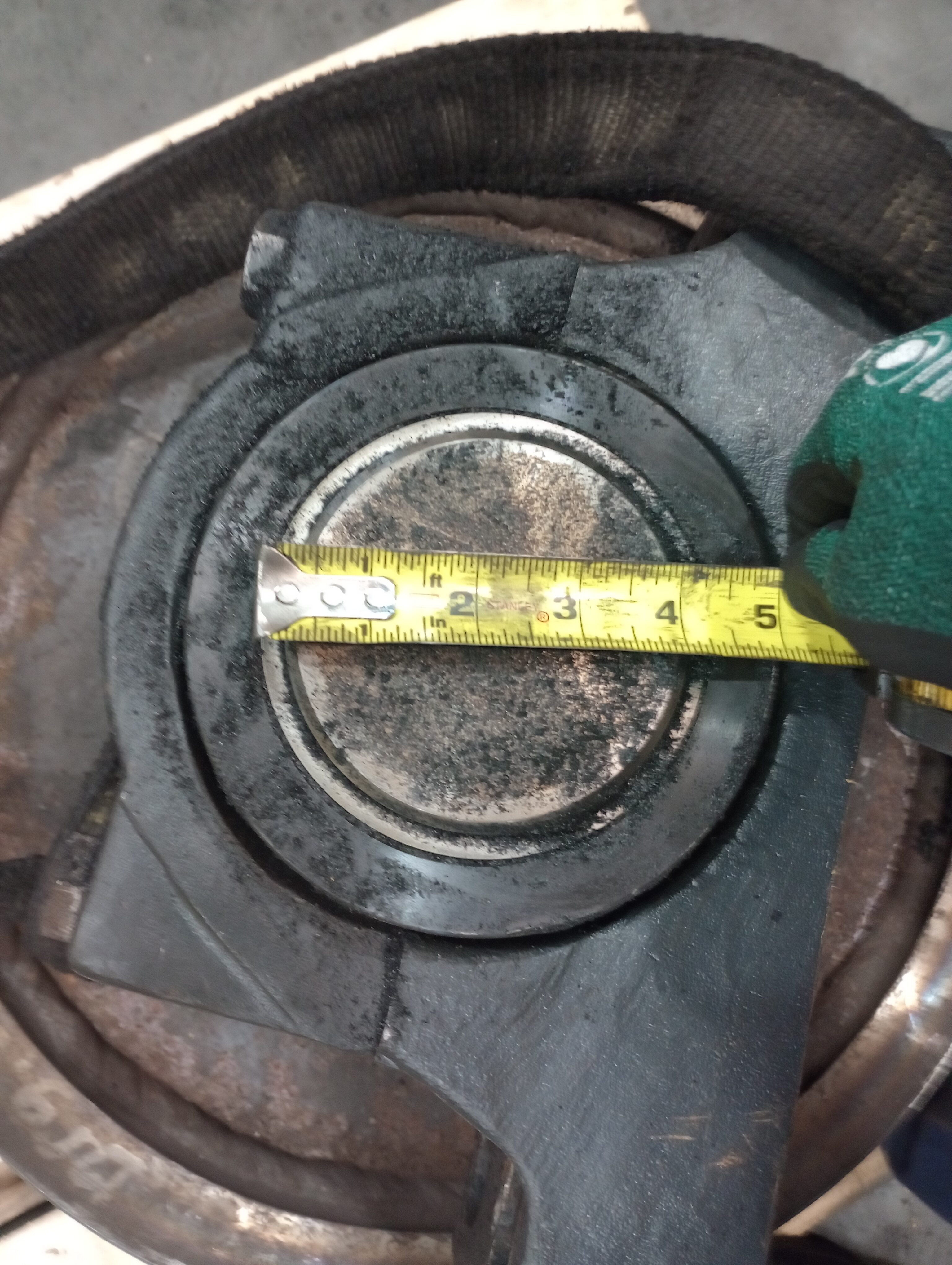
Do you have any idea how much force it takes to break something like that in half?
A Lot doesn’t begin to cover it.
Yet somehow, some way, someone figured out how to do that today.
More than likely not on purpose but there it is.
This is the kind of shit I get to deal with on occasion.
I won’t even tell you what it took to get apart and set on the ground, it was eight feet up.
Still beats the shit out of sitting in a cubicle all day though.
My husband can break anything and everything. That’s why I call him wreak-it Ralph. But then again the Marines trained him for years to kill people and break things. Lucky girl that I am, he can fix near everything. Plumbing, electrical, gas fitting, mechanical systems, HVAC, vehicles, appliances, etc. Counting my blessings.
Repetitive stress w/ crystallization fracture?
From looking at the shaft in “normal” light, I’d venture to guess you got in one. Bunk.
Is that a con rod for a stamping press? Looks pretty massive.
It’s for a big roller at the end of a gantry that holds down one of those 50,000 pound rolls of steel as it is unwound to flatten it.
You haven’t worked on an oil rig with new hands I take it? Lol
My cell has a special ring for the ops supervisor at one of our plants. When it goes off i always answer it with “what did you break now”
Usually someone thought a valve was too loose and tossed a snipe on it. We cut out and replace dozens of valves a year were ops sheared the shaft off.
How old is it or how long has it been in service and what kind of machine is it in?
As a mechanical engineer, Irish can probably calculate the amount of force it took to break that, unless it was there waiting to happen all along because of bad heat treat during/after forging or after machining. Another possibility is heat stress or impact fatigue over time.
What kind of machine is that? Inquiring minds want to know.
See my answer above.
Yeah, we have big equipment that turns at high torque, 24 hrs a day, 7 days a week, 52 weeks a year. And occasionally the machine just has a fricking come-apart. Usually pretty impressive when it happens. Hell, we even put vibration monitors on stuff and still it catches us by surprise. I’m advocated that we totally abandon our test-n-inspect program, generally stuff fails about 2 weeks about the T&I guys give it a clean bill of health. Instead, we ought to just “run to failure” since that’s what happens anyway.
The only really amazing thing is just how fast we can get a new shaft machined, installed, and running again.
Start tracking failures and hours. I would suspect that if you looked your mean hours between failures is pretty consistent. Then you just set replacement based on that and have a pm for changing it at X hours.
Works for aircraft of all types, why not for ships? MTBF is there for a reason!
That’s what the textbook answer is, but I’m a chemical engineer, not mechanical so that distinctly falls under “not my job”. I’ve gotten pretty good at that in my 35+ years of working this industry.
In reality, we’ve done that MTBF study and it does vary, wildly. I personally think some of it is the total number of start-stop cycles, plus hours run time. The starting under a load really puts the machine in a bad way.
Most of the things that come into the shop with broken shafts are due to lack of grease. “I didn’t know there were grease zerks on there”. Well did ya look? Or “I saw the bolts were loose” and you didn’t tighten them?
Crankshaft from a shear? Also, a lot of wear in that connecting rod.
I don’t know much about metallurgy, stress fractures, etc. But I’d go back to being a cubicle dweller any day, compared to what I’m doing now. I made wicked money back in those days. Even not adjusted for inflation, making half of what I made back then would be an improvement.
I don’t know how you do it, Phil. My tired old body would sure be giving me hell if I tried to do what you’re doing.
And this morning’s fun. SNOW! Fuck.
Yeah, I’ve seen stuff like that, and worse. Shafts broken because of improper alignment of gearboxes and overloading of the machine are common. A few years ago, customer had been overloading and plugging a machine with a 7″ diameter shaft and eventually broke it. Then they went out and had a local machine shop replace the shaft, using a lesser grade of steel. Lather, rinse and repeat for a several cycles of this retardation before calling to say “your” head shaft keeps breaking and oh, no we NEVER overload or plug the machine. Yeah, right. I went out to have a lookit and the first thing the operators told me was, oh yeah, we plug the &^%$#@! out of that &^%$#@! all the time. Good times.
Phil will verify anybody who messes with machinery has a photo file chock full of such misadventures. I call mine my “little shop of horrors”.
Looks like the main crankshaft on a 500 Ton mechanical press we had at my workplace 25 years back.4 ft thick floors and it shook the building each cycle.
OK, a little lesson, Torque overload failure would be at 45 degrees to image plane. Bending failure would be as seen. The light grey colored ring is where the bearing surface heat treat is. The dark grey is the virgin unheatreated material. It is too dirty to tell but a shaft not in alignment would be subjected to repeated bending loads. Over time these would propagate from a small surface defect (pit in bearing surface) and cause a series of partial rings to be seen as “beach marks” (think waves leaving lines on the sand from a receding tide). If it is a punch press crankshaft then the load would be in the same place for each punch cycle. If there are no crack origination indicators then the failure is from a single cycle overload. Think mismatched die halves. Lucky is no one died.
Spin
BSME, University of Minnesota Institute of Technology
PS: all solid metals are crystals.
Good correct analysis, Spin. I wasn’t going to go into particulars since I’m not trained in stress failure analysis, although I’ve seen a lot of analysis pics.
My specialty, such as it is, is making SWAGS…
At my last job, I was the guy they called to figure out what the hell went wrong. If I fixed it it stayed fixed until some knuckle dragger single helix decided to improve on the solution. I’ve even had the President of the company do the opposite of what I told him and turn a $80,000 dollar field fix into a quarter million campaign. Now since Phil has said it is a shaft, my bet is that the shaft support bearings have worn enough to let the shaft, now unsupported, to wobble from just the gravity load and have a rotating stress field form in the shaft itself. Doesn’t take too long after that. And yes PM is the only way to go.
Spin
I would review all previous maintenance and repairs to the machine as well as the drive system for wear and damage. When someone complains that engineers design stuff to fail, they are actually correct: the universal joints and couplers fail first/require the primary maintenance, and everything else in the system as you work up to the big ticket items (in the example of a truck: u-joints, then clutch, then yokes, then driveshafts, then input/output shafts and finally transmission or differential.)
Believe it or not, those guys do have most of the stuff figured out.
Most importantly, is it fixed, or will be, in short order?
There’s the rub. God put you in that spot to make it go again!
Not as impressive as a 4” steel shaft (Jesus), but knew a guy that snapped a half-shaft from a stock late-90’s Honda Civic. If I remember correctly, he said he was making a turn, then all of a sudden it was noisy and wouldn’t steer worth a damn. No idea how he managed it…
well, depending on how long that shaft is, you might want to cut a couple of 12-18″
bits, a buddy’s dad did that years ago and made a couple of black powder cannons on of it. bored out to fit a beer can. now, it takes a while to do this.
but the end result can and is a lot of fun. we used to lob cans filled with concrete
across the coal stripping back in the day- late 1960’s
I think, he got the steel from a old rail road axel . I think it was.
the side bits where big ass bolts that where screwed in and welded in place.
it is neat to have your very onw cannon. I have one. it bronze alloy.
Hehe
?? years ago a welder friend had to do a temporary “patch job” on a hydraulic ram on a car crusher that somehow snapped. (still suspect a loose control nut) Grind it out and then fill it with weld & then they did a rough turn on a lathe. It apparently held up enough until a real replacement arrived. They only lost a day or 2 of work.
Nothing is ever really idiot proof.