I finally got off my dead ass and did some more work on the Sprite floorboard project today.
First I went and bought some spray on rust converter and then I cleaned all around where I cut the floor out with acetone before spraying it on all around the hole. Then I sprayed the patch piece with some Weldable Primer I ordered a couple of weeks ago.
After that I also sprayed it around the inside of the car where it is going to be welded on.
After all that, I slid the patch into place and had the Wifely Unit come out and press down on the patch piece because it’s a bit warped from the manufacturer while I slid underneath and traced the edge of the cut out so I could see where I needed to drill all the holes so I can spot weld it into place.
Then of course all the drilling etc.
Then I cut out around the rear spring perch bracket and got it final fitted and ready to weld in with one more final coat of primer on the patch.
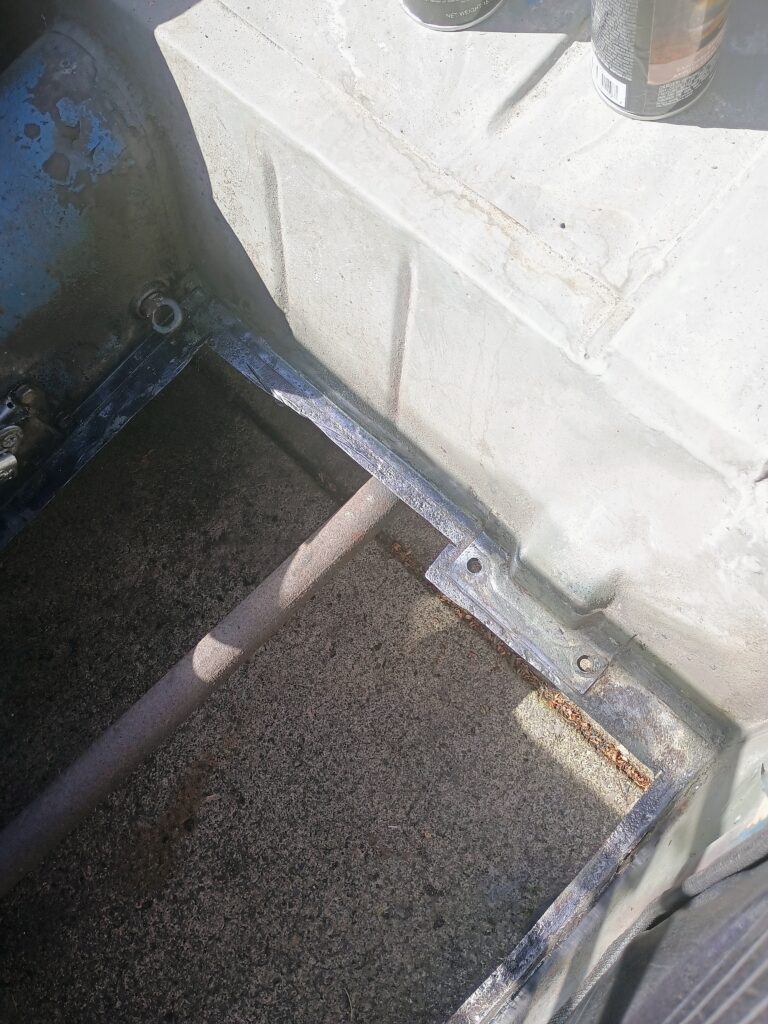
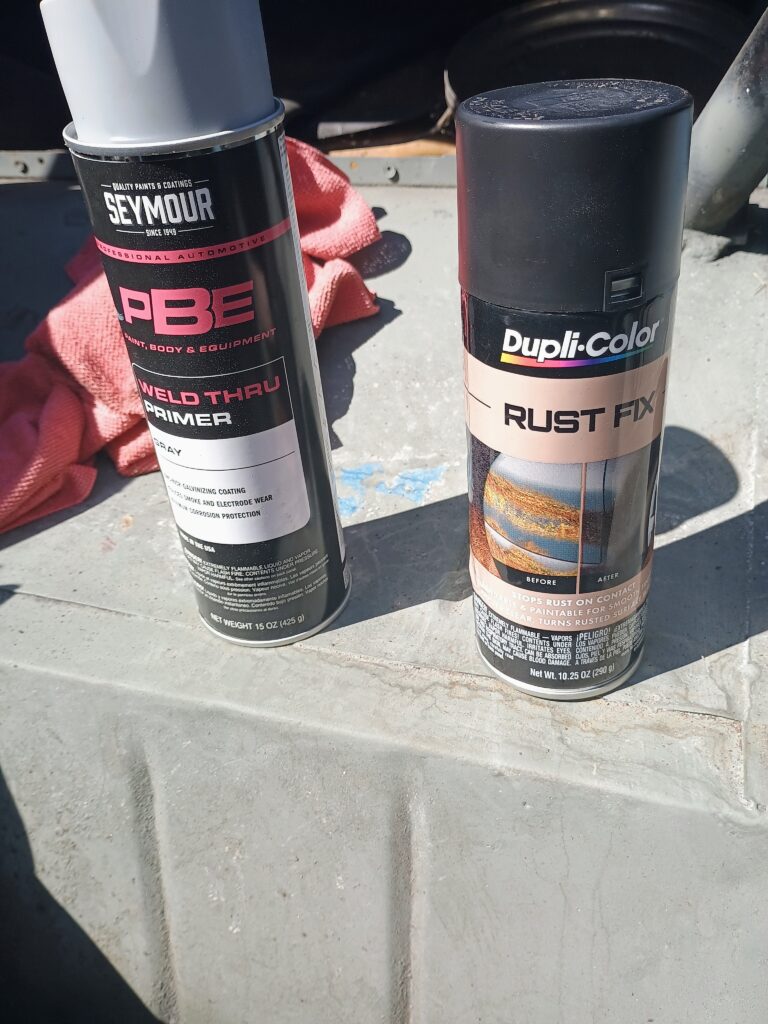
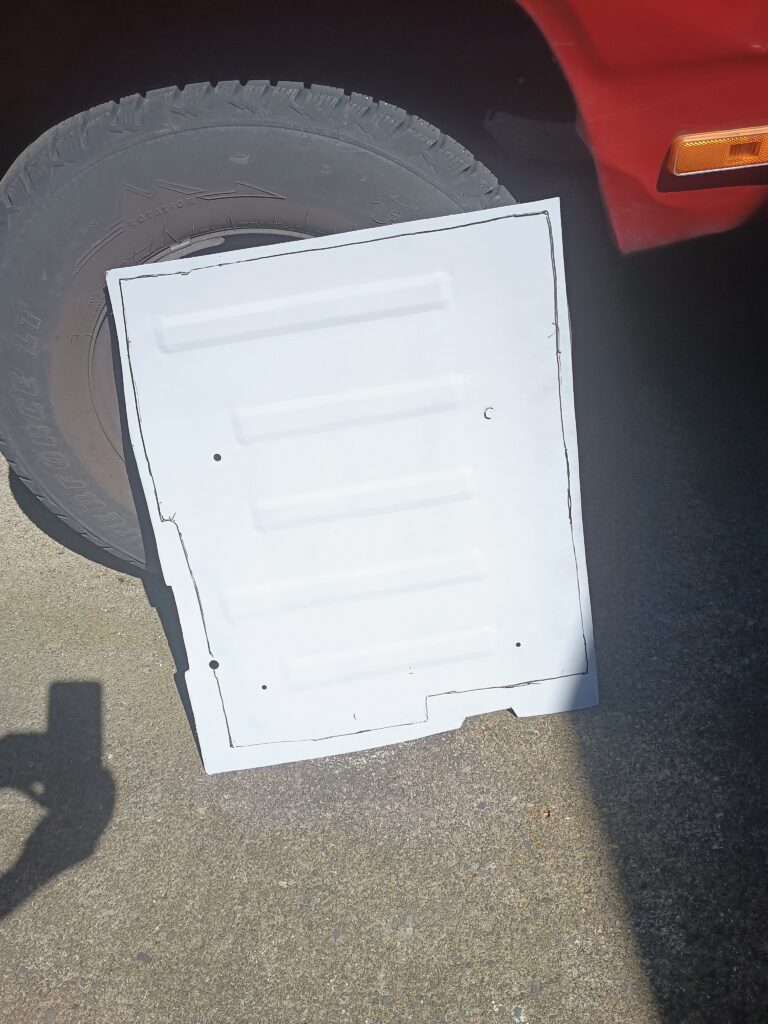
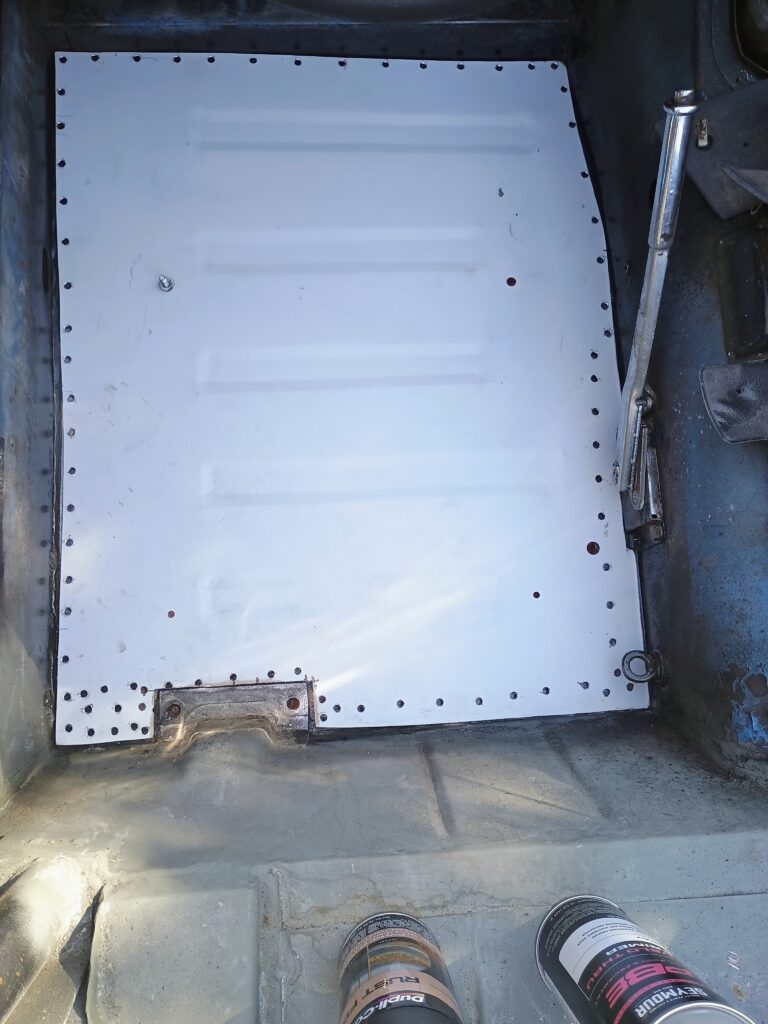
I have a doctor’s appointment tomorrow. Depending on the weather I might actually get this welded up before Friday.
We shall see.
I remember doing this job with the Mustang minus the weldable primer. This was 40 years ago. It was a 66 coupe with a 289 that I dropped a crate 302 into. I replaced the interior and added sound deadening under the new carpet. It was a no AC car in south Georgia with headers that heated up the floorboard. I sold the car for about $300 more than I had in it.
years ago, I bought a HTP welder with spot weld function. it was hands down the fastest way I ever used to fill in thousands of spot weld holes like you have there.
although I did end up buying a Miller spot welder for the harder ones after a while.
started out using a soft copper back up plates until I bought the HTP welder.
I think they called “Weld America” now a days. it was a great welder and easy on the electric bill too compared to my old Hobert welder.
the miller spot welder is handy for some work if you buy the right “tongs” for it.
I have 3-4 sets of “tongs” in my shed for the Miller. funny thing, I tried to sell it after blowing out my back. no one wants to pay Miller prices for it. they all offer harbor freight prices instead. I tell them to go and buy a Harbor freight one instead ! why should I sell it for less than 1/4 of what I paid for it ?
after all it not like I have to feed it or something.
you might want to jump around when welding up the holes to keep any warping
of the sheet down. or are you going to clamp the hell out of it in place ?
still you will have to do something about the heat build up with that many welds
so close together. compressed air works or maybe ice cold rags.
I had better luck with the cold rags than compressed air myself.
either way, you going to have to take your time with it. good luck !
and take it easy on yourself too. these things always seem to take a lot longer than you would like.
and after you get it welded in place, you still going to want to use some kind of seam sealer around it. just to keep any water out of it. something like the kind of tar like crap you had to remove to get this far with it. whatever it is, it was used on a lot of old English sports cars back in the day. kind of weird after spending hours on some small section of the car, you step back and realize you have hours more work ahead of you to finish. still, it kept me out of the bars and other stupid places back then. one thing you do realize is you end up wishing they still made cars and trucks as simple as they did back then. before all the junk they have now on “modern” cars. hell, even my old 1994 4runner is a lot worse than any old car/truck made in the 1960’s with all of the computer control crap in it.
Good for another 75 years, right??
Looks great! You’ll be back on the side of the road in no time!
Yeah, well done Phil. Tight.